Cuidados del turbocompresor del motor
Por Gustavo Zamora* para gruasytransportes, Buenos Aires (Argentina).
En los buques y en las estaciones generadoras de energía, donde se exige una muy alta disponibilidad al motor diesel. Los turbocompresores del motor diesel son recorridos, esto es reparados a nuevo, en base a la cantidad de horas de operación y no en base a su condición.
En los motores diesel auxiliares que funcionan como generadores en los buques, se repara el turbocompresor a nuevo y se cambian sus rodamientos durante el mantenimiento programado de las 8.000 horas (1).
Algunos usuarios de motores MAN, Mercedes Benz y MTU de entre 400 y 1.000 HP de potencia, cambian los turbocompresores y luego los hacen reconstruír a nuevo cada 4.000 o 5.000 horas de trabajo.

1 Crédito: diariomotor.com.
* Consejos para alargar la vida útil del turbocompresor
Existen tareas de mantenimiento preventivo que se pueden realizar, tales como una descarbonización del turbo o una comprobación de holguras en su eje. No obstante, lo mejor para evitar que el turbo se vaya al cielo de los turbos es seguir estas pautas:
– Espera un par de minutos al arrancar el motor diesel y también antes de parar el motor diesel, manteniendo el motor funcionando en ralentí y si no es posible tener el motor en ralenti espere con el motor a velocidad nominal pero sin carga. Esto normalizará la temperatura del turbo y evitará que el aceite del eje se carbonice, creando sedimentos y partículas abrasivas que darán al traste con el carrete y provocarán fugas de aceite. Las paradas tras una conducción a máxima carga son especialmente delicadas.
– Utilice aceite de máxima calidad. Parece una obviedad, pero lo cierto es que el ahorro en aceites baratos – con propiedades lubricantes inferiores y deterioro rápido – queda completamente anulado por una rotura del turbocompresor antes de tiempo.
-No acelere el motor ni lo cargue hasta que el aceite no esté a la temperatura óptima. Cae de cajón, quieres asegurarte de que las propiedades de lubricación del aceite sean perfectas, y la viscosidad adecuada. Esto también beneficia al resto de componentes de fricción del motor.

2 Turbocompresor roto. Crédito: diariomotor.com.
* ¿Qué debo hacer en caso de avería del turbocompresor?
Si tu equipo lo permite para el motor de inmediato y evita males mayores como doblar una biela del motor o sacar una biela por el costado del block del motor. Los mecánicos reemplazarán el turbocompresor. El turbo volverá a funcionar adecuadamente tras la reparación. La integridad física del motor no se vería comprometida si la reparación estuvo bien realizada. (2)
Siempre es más económico reparar un turbo que comprarlo nuevo. En cuanto empecemos a notar síntomas de fallo (silba demasiado, falta de potencia, humo azulado, consumo de aceite…) es mejor revisar su estado y comprobar si tiene holgura axial antes de que se averíe definitivamente. Un eje desgastado acaba siempre en rotura y un turbo al romperse puede destrozar el motor por completo. Comprobar la holgura del eje del turbo no suele llevar más de una hora de mano de obra, y ese trabajo es un “regalo” comparado con las consecuencias de la rotura.
Es, entonces, mejor comprobar su estado antes de que se rompa por completo.(7)
* Falla del evaporador de gases de motor

3 Filtro del evaporador de gases (PCV). Crédito: turbo-matic.com
En muchos motores diesel, uno de los fallos frecuentes es la avería en el filtro evaporador de gases de motor, que suele estar compuesto por una válvula o membrana y por un filtro.
Nos podemos encontrar con que el filtro esté obstruido o petrificado por acumulación de carbonilla y que la válvula o membrana esté perforada y no actúe. En cualquiera de los dos casos, la avería se traduce en un fallo en el sistema de recirculación de vapores de motor.
Como consecuencia, nos podemos encontrar con que pase aceite hacia el circuito de aspiración de aire del turbocompresor, lo que puede provocar que el aceite llegue al sistema de admisión del motor y se cree autocombustión por ingestión de aceite. Y también, por otro lado, se puede crear una sobrepresión de gases de motor, que al no ser evacuados por el evaporador, pueden provocar daños severos en el turbocompresor e incluso en el motor. (3)
* Veamos a continuación qué dice el boletín de información técnica para el reemplazo del interenfriador – o intercooler- después de una avería del turbocompresor publicado en inglés por Behr Hella Service GmbH:
* Reemplazo del intercooler después de una avería o falla del turbocompresor
Puntos generales
Casi todos los motores diesel modernos con turbocompresor tienen un Intercooler -o interenfriador-. El aire caliente (con hasta 150 °C) comprimido por el turbocompresor es luego enfriado por el intercooler (Fig. 1) antes de llegar a la cámara de compresión. El aire comprimido es enfriado por el aire ambiente del exterior (interenfriamiento directo) o es enfriado por el refrigerante del motor (interenfriamiento indirecto).
La configuración y la función de los dos sistemas se muestra en más detalle en la hoja de información técnica «Intercooler».
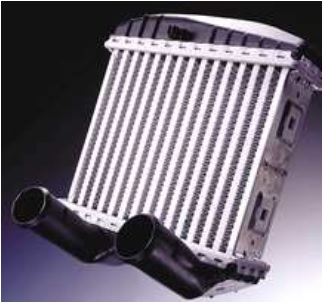
Fig. 1. Crédito: behrhellaservice.com.
* Razones para tener una avería y sus consecuencias
Junto a las razones clásicas para la falla o avería tales como
- Daño externo (accidente, lanzamiento de grava o tierra dentro del turbocompresor).
- Mangueras dañadas / bloqueadas.
- Caudal de aire reducido debido a la superficie del filtro con suciedad.
- Pérdida de refrigerante o del aire secundario que trabaja en el intercooler debido a fugas.
- Un pobre intercambio de calor debido a la suciedad interna del intercooler (depósitos calcáreos o agentes selladores).
Existen otras posibilidades que también deben ser consideradas. Estas están relacionadas generalmente con la avería del turbocompresor.
En el caso de daños mecánicos al turbocompresor (Figuras. 2 a 5) o en caso de una fuga de aceite en el lado del compresor, el aceite y las virutas pueden acumularse
en el intercooler. El hecho de que este ensuciamiento / bloqueo puede conducir a una caída en el rendimiento del motor diesel es lo menos dañino que puede ocurrir. Las cosas se vuelven mucho más serias cuando el aceite o la viruta salen del intercooler y entran en la cámara de combustión. Esto a menudo conduce a una avería o falla del motor. Algunos motores sufren un episodio de sobrevelocidad – en inglés, «overrev»-, es decir que aumentan sus RPM hasta quedar destruídos después de que el turbocompresor ha sido reemplazado.

Fig. 2. Crédito: behrhellaservice.com.
Se puede llegar a acumular tanto aceite en el intercooler que conduzca a que este aceite se autopropulse repentinamente hacia la cámara de combustión después de la instalación del turbocompresor nuevo, que fue colocado para volver a tener la presión de sobrealimentación correcta.
En caso de que eso suceda cualquier especialista puede imaginar lo que acontece poco después que el motor se ha puesto en marcha. Para prevenir tal daño, como así también el «daño subsiguiente» (esto es que las partículas de metal se liberan luego en el intercooler y entran luego a la cámara de combustión), el intercooler y las piezas de fijación siempre deben ser examinados cuidadosamente cada vez que se reemplaza un turbocompresor.(4)
* En caso de que los cilindros estén inundados con aceite:
El motor de arranque puede verse impedido de hacer girar el motor por una causa ajena al motor en sí. El aceite pudo llegar a los cilindros e inundarlos. Esto puede producir daños severos en el motor al intentar arrancarlo, como por ejemplo doblar una biela.
La solución es sacar los inyectores ANTES DE INSTALAR EL TURBOCOMPRESOR NUEVO y hacer girar el motor con el motor de arranque durante 10 a 15 segundos sin que el motor arranque -o sea con el paso de combustible cerrado-, hasta que el aceite haya sido expulsado totalmente desde dentro de los cilindros.
Luego reinstalar los inyectores y purgar la línea de combustible. (5)y(6)
* Durante la instalación de Turbocompresor:
Es importante que durante todo el proceso de instalación del turbocompresor, se evite la entrada de suciedad o de elementos extraños a ninguna parte del turbo.
Cualquier suciedad o elementos extraños que entren al turbocompresor pueden causar daños catastróficos debido a la muy alta velocidad de operación del mismo (hasta 300.000 rpm). (6)
* DESPUES DE INSTALAR EL TURBOCOMPRESOR NUEVO:
-Debemos volver a hacer girar el motor con el motor de arranque durante 10 a 15 segundos sin que el motor arranque -o sea con el paso de combustible cerrado- esto ayuda a purgar/cebar el circuito de lubricación de aceite al turbocompresor al llenar las tuberías de presión de aceite de lubricación, el filtro de aceite y el turbocompresor con aceite antes de la puesta en marcha. Nota importante: tan pronto como el
el motor arranca, el turbo funcionará a alta velocidad y la falta de lubricación en estos
primeros segundos vitales pueden destruir un turbocompresor nuevo.
(5)y (6)
* Continuando con lo explicado en el boletín de información técnica para el reemplazo del interenfriador – o intercooler- después de una avería del turbocompresor publicado en inglés por Behr Hella Service GmbH:
* Motivo del daño, prueba de componentes
En el contexto de la sustitución de un turbocompresor, el motivo de la avería siempre debe ser investigado. De lo contrario, el turbocompresor podría fallar de nuevo en muy poco tiempo.
Deben ser atendidas las normas de instalación provistas por los fabricantes tanto del turbocompresor como del vehículo.
Aquí hay algunos ejemplos:
- Verifique las válvulas de control y/o de conmutación y las tuberías de vacío
- Verifique la tubería de admisión de aire y la tubería colectora de gases de escape en búsqueda de impurezas / residuos y límpielas de ser necesario
- Verifique el filtro de aire y reemplácelo de ser necesario.
- Reemplace la tubería de suministro de aceite al turbocompresor (una
inspección visual o una limpieza no son suficientes).
- Verifique la tubería de retorno de aceite, límpiela, y reemplácela si tiene dudas
(las impurezas pueden entrar en el cárter de aceite y luego ser succionadas de nuevo por la bomba de aceite).
- Lleve a cabo un cambio de aceite del motor y un reemplazo del filtro de aceite del motor.
- No utilice agentes selladores líquidos.
- Llene previamente con aceite el orificio de entrada de aceite del turbocompresor antes de ponerlo en funcionamiento.
- Compruebe / limpie toda la ruta del aire entre el turbocompresor y el
motor.
- Verifique que el intercooler no tenga residuos de aceite / impurezas, reemplácelo
si es necesario.

Fig. 3. Crédito: behrhellaservice.com.

Fig. 4. Crédito: behrhellaservice.com.

Fig. 5. Crédito: behrhellaservice.com.
* Limpieza del intercooler
La limpieza del intercooler es extremadamente problemática.
Hay diferentes opiniones sobre esto en el mercado. En muchos casos, el fabricante del equipo recomienda el reemplazo del intercooler. El intercooler siempre debe ser reemplazado en el caso de daño mecánico al turbocompresor (por ejemplo, paletas o álabes dañados, Fig. 2 a 5). No se puede garantizar que las virutas se eliminen completamente cuando se lava y enjuaga el intercooler, particularmente en el caso de intercoolers con insertos de turbulencia (Fig. 6). El riesgo de un daño posterior causado por las virutas que se liberen y sean succionadas en dirección hacia dentro del motor con posterioridad a la limpieza del intercooler es simplemente demasiado grande.
La limpieza del intercooler solo puede ser considerada como válida, si el único problema es que el aceite de motor se ha acumulado en el intercooler (Fig. 7). En la práctica, sin embargo, el lavado del intercooler es extremadamente complejo. Particularmente cuando se trata de grandes tuberías, como las que se encuentran en los camiones y grúas. Además, solo se pueden usar líquidos de lavado aprobados por el fabricante del vehículo y/o del componente. El uso de líquidos de limpieza inadecuados puede provocar daños materiales y la pérdida de la protección de la garantía.

Fig. 6 y Fig. 7. Crédito: behrhellaservice.com.
* Notas sobre la instalación de un intercooler nuevo
No importa cuál sea el motivo de la falla o del reemplazo del intercooler. Antes de la instalación de la nueva unidad, se debe investigar a fondo el motivo del daño. Las partes periféricas (turbocompresor, ventilación del cárter, recirculación de los gases de escape, entrada de aire al turbocompresor, sistema de escape, etc.) deben integrarse en el proceso de búsqueda y solución de fallas/problemas.

Fig 8 Circuito Turbocompresor Intercooler. Crédito: behrhellaservice.com.
De lo contrario, una falla puede volver a ocurrir. Por esta razón, se deben considerar los siguientes puntos:
• Verifique el recorrido del aire entre el turbocompresor y el intercooler buscando impurezas / partículas / bloqueos / reducciones en las secciones transversales.
• Compruebe el recorrido del aire entre el turbocompresor y el colector de admisión buscando impurezas / partículas / bloqueos / reducciones en las secciones transversales.
• Limpie / reemplace la canalización de aire dañada, bloqueada o sucia y sus piezas de fijación.
• Reemplace las juntas de las tuberías de aire, las conexiones de refrigerante (en el caso de los intercoolers refrigerados por agua) según sea necesario.
• Asegúrese de que todos los elementos de conexión estén apretados, que no se produzcan fugas y no se aspire «aire secundario» dentro del circuito de “aire primario”.
• Verifique la presión de sobrealimentación.(4)
* Veamos a continuación qué dicen las Recomendaciones generales para instalar un turbo publicadas por Turbo Diesel de Colombia Ltda.
Puntos de inspección y verificaciones:
-. Verificar si el Turbo corresponde a la aplicación para la cual fue diseñado.
-. Se deben cambiar los filtros de aire y aceite, así como el aceite lubricante de motor por otros totalmente nuevos y por ningún motivo debe utilizarse aceite reciclado.
-. Inspeccionar los sistemas de entradas y salidas del turbo para asegurar la ausencia de materiales indeseables como: fragmentos de mecanizado, virutas, tuercas, arandelas, pedazos de manguera, etc. Tenga en cuenta que partículas muy pequeñas pueden causar daño en el eje turbina o la rueda compresora. Verificar el estado de las mangueras y abrazaderas.
-. Los múltiples de escape, mangueras o tubos de entrada de aire y retorno de aceite tienen que estar totalmente limpios, sin dobladuras ni escapes.
-. Desmontar y lavar el intercooler (Solo si aplica).
-. En la entrada y salida de los turbos se deben utilizar empaques originales no permitiendo el uso de pegantes ni Silicona.
-. Verificar que los tornillos, espárragos, el múltiple se encuentren en buen estado, que no estén averiados o con fisuras. En caso de detectarse fallas se deben cambiar.
-. Colocar aceite limpio dentro del turbo y hacerlos girar manualmente. Esto con el fin de prelubricar los componentes internos. NUNCA SE DEBEN FRENAR LOS ROTORES DEL TURBO AL MOMENTO DE ENCENDER EL MOTOR, ya que se puede aflojar la tuerca y ocasionar daños internos.
-. Al montar el turbo cuidar que el drenaje de aceite quede los mas vertical posible.
-. Verificar que todos los tornillos de fijación del turbo se encuentren debidamente apretados. Verificar nivel de agua y de aceite.
-. Después de completada la instalación del turbo al sistema, poner en marcha el motor y mantenerlo operando a marcha mínima durante 5 minutos. No acelerar el motor.
-. Estando el motor en marcha tapar el lado de admisión de aire y verificar que el motor se apague al instante, si esto no ocurre, inspeccionar fugas en el sistema de entrada de aire.
* NOTAS IMPORTANTES:
– La tuerca del extremo del lado del compresor no debe tocarse. De hacerlo se romperá el sello adhesivo que la fija y desbalanceará el conjunto provocando la distorsión del eje.
– La bomba de inyección debe estar calibrada según las especificaciones del fabricante del motor. El exceso de combustible provocará el desgaste prematuro del turbo y del motor.
* RESPETANDO ESTAS INDICACIONES EL TURBOCOMPRESOR Y EL MOTOR TENDRÁN UNA VIDA MÁS LARGA, EVITANDO PARADAS INDESEABLES Y COSTOS ADICIONALES.(8)
Descargue este artículo en español en pdf: Cuidados del turbocompresor del motor
Bibliografía- Referencias:
(1) brighthubengineering.com/marine-engines-machinery/66033-maintenance-schedule-for-marine-auxilliary-diesel-engines/
(2)
diariomotor.com/page/2/
(3) turbo-matic.com/averias-turbos-comunes
(4) Technical Information Replacing the intercooler after a turbocharger fault – Behr Hella Service GmbH behrhellaservice.com/behr-hella-service/assets/media/ti_en_airco_ladeluftkuehler_turboschaden.pdf
(5)
cmelectronica.com.ar/noticias/como-identificar-fallas-en-un-motor-marino-diesel.html
(6)TURBO InstallatIon InstructIons: General – Garrett By Honeywell
garrett.honeywell.com/wp-content/uploads/2013/10/Turbo_Installation_91913.pdf
(7) autocasion.com/actualidad/reportajes/cuales-son-las-averias-y-cuidados-del-turbo
(8) turbodieseldecolombia.com/gallery
Fuentes:
Texto compilado y traducido de gruasytransportes < gruasytransportes.wordpress.com>
(*)Gustavo Zamora es un especialista en equipo de elevación y manejo de cargas. Vive y trabaja en Buenos Aires (Argentina).
Tags: turbocompresor roto aceite en la admisión motor diesel (gz11), Hydrolock=cilindros inundados con aceite o con agua que se opone a la fuerza del motor de arranque y debido a ello se doblan una o más bielas, cómo evitar romper el motor por culpa del turbocompresor, 800.000 kilometros = 500.000 millas = 15.000 horas de operación, turbodiesel buenos cuidados, cooling down to stop, el motor diesel turbo debe girar en ralenti 30 segundos como mínimo antes de parar el motor, si el motor se ha calentado en exceso (recalentamiento) siempre se le debe cambiar el aceite y el filtro de aceite de motor antes de volverlo a operar una vez reparada la causa del sobrecalentamiento, mayor presion de sobrealimentación mayor potencia del motor pdf (gz22), en algunos motores MAN, Mercedes Benz y MTU de entre 400 y 1.000 HP de potencia se pueden lograr 14.000 horas de uso en los turbocompresores inspeccionando periódicamente el turbocompresor y revisando sus huelgos,
Si quiere colocar este post en su propio sitio, puede hacerlo sin inconvenientes,
siempre y cuando no lo modifique y cite como fuente a https://gruasytransportes.wordpress.com
Recuerde suscribirse a nuestro blog vía RSS o Email.